TOC理論とは?考え方や導入のメリット・注意点をわかりやすく解説
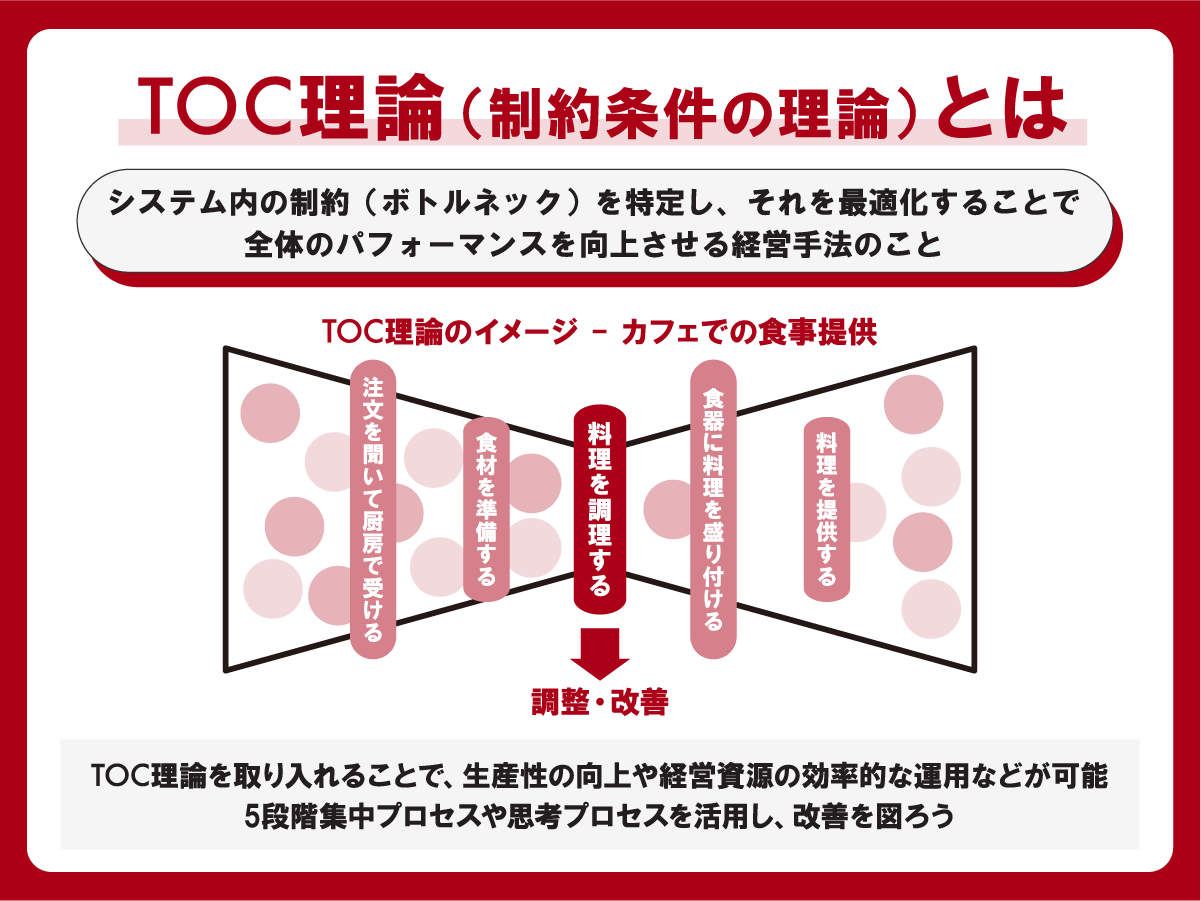
TOC理論は、製造プロセス上のボトルネックを特定・改善する手法として知られており、経営課題の解決手法の一つとして、組織や業務のパフォーマンス最大化にも活用できます。本記事では、TOC理論の基本的な考え方や経営に導入するメリット、注意点などについて、製造業界の専門家が解説します。
TOC理論は、製造プロセス上のボトルネックを特定・改善する手法として知られており、経営課題の解決手法の一つとして、組織や業務のパフォーマンス最大化にも活用できます。本記事では、TOC理論の基本的な考え方や経営に導入するメリット、注意点などについて、製造業界の専門家が解説します。
目次
TOC理論(制約条件の理論)はシステム内の制約を特定し、それを最適化することで全体のパフォーマンスを向上させる経営手法です。エリヤフ・ゴールドラット氏によって1980年代に開発され、ボトルネックがプロセスや組織のパフォーマンスを制限するという考えにもとづいています。
TOC理論はボトルネックとなっている課題を解決して全体的なシステムの効率を向上させることを目的としており、製造工程の最適化・プロジェクト管理・サプライチェーン管理などさまざまな分野で応用されています。
TOC理論を理解するための身近な例として、カフェで食事を顧客に提供するプロセスを想像してみましょう。
カフェでは顧客から注文を受けてから料理を提供するまでに、以下の複数のステップがあります。
TOC理論では、まずこのプロセスのどこかに「ボトルネック(制約)」、つまりスムーズな慣れを妨げているポイントがあると仮定します。
例えば、調理場の担当者が一人しかいないため、調理に時間がかかるというボトルネックを想定します。調理場での作業能力は、料理の提供はもちろんカフェ全体のサービス提供速度を制限していると考えられるでしょう。
次に、この制約をどう改善するかを考えます。改善例として、例えば以下が挙げられるでしょう。
これらによって、カフェの全体的な業務効率が向上し、より多くの顧客に迅速にサービスを提供できるようになります。
この例のように、TOC理論は組織やプロセス全体を見渡し、最も効率を低下させているポイントに焦点を当てて改善をおこなうことで、全体のパフォーマンスを向上させる手法です。
手法 | 観点 |
---|---|
トヨタ式生産方式 | 生産工程の無駄を排除 |
TOC理論 | ボトルネックを特定 |
トヨタ生産方式とは、生産工程の無駄を極力排除し、効率的で柔軟な生産体系を実現するための手法です。TOC理論とは特にプロセス全体の無駄を排除することに重点を置いているという点で異なります。
トヨタ生産方式は、必要な部品を必要なときに必要な量だけ供給するジャストインタイム(JIT)生産やカンバンシステムを採用することで無駄を削減し、在庫コストの削減と生産効率の向上を図ります。
一方、TOC理論はシステムの成果を最大化するために、システム全体のボトルネックを特定し、それに焦点を当てる方法です。
手法 | 観点 |
---|---|
DBR | 生産のペースに焦点を当てる |
TOC理論 | システム全体のボトルネックに焦点を当てる |
DBR(Drum Buffer Rope:ドラム・バッファー・ロープ)とは、TOC理論の枠組みのなかで開発された具体的な生産管理手法です。DBRはTOC理論の一部であって、生産管理に焦点を当てた手法である点が異なります。
DBRでは、生産のペースを制約に合わせ(ドラム)、余裕を設けて不測の事態に備え(バッファー)、ボトルネックの前後の工程の制限(ロープ)を設けることでプロセスを統制します。これにより、システムの制約を中心に全体の生産効率を最適化します。
一方、TOC理論はより広範な思考フレームワークであり、システム全体の制約を特定し、ビジネスや生産プロセス全般の問題解決や改善を目指します。
TOC理論を適用して改善をおこなう際は、フレームワークを使って実践するのが一般的です。
TOC理論を用いて問題解決をおこなう主なフレームワークには、5段階集中プロセスを利用した手法と思考プロセスを利用した手法の2種類があります。どちらの手法も、問題の性質と組織のニーズに合わせて選択されます。
TOC理論の問題解決手法 | 使い分けの観点 |
---|---|
5段階集中プロセスを利用した手法 | 明確な物理的制約が存在する場合 |
思考プロセスを利用した手法 | 心理的な制約など、明確な物理的制約がない場合 |
5段階集中プロセスは、例えば製造設備の容量不足などのように物理的な制約による明確なボトルネックが存在し、全体のパフォーマンスに大きな影響を与えている場合に適しています。
思考プロセスはより複雑で系統的な問題、特に組織内の方針や戦略、心理的な制約など、背後にある原因や論理的な構造を探る際に適した解決手法であり、明確な物理的制約がない場合に特に有効です。
5段階集中プロセスは、システムやプロセスの効率を最大化するためにボトルネックを特定し、集中して改善を図るTOC理論のフレームワークです。
5段階集中プロセスは、制約の特定から最適化、必要に応じて制約の改善や新たな制約の特定に至るまでを一連とした五つのステップを含みます。
以下では、それぞれのステップについて事例を交えながら解説します。
システムのパフォーマンスを制限する制約条件を見つけるステップで、システム内のボトルネックや問題点を特定します。目標は、全体の流れに最大の影響を与えるポイントを見つけ出すことです。
例えば、食品加工メーカーで1日の出荷スピードが目標に達していない問題が発生していると仮定します。
まずは「パッケージングラインがフル容量で稼働しているか」「無駄な時間や資源が使われていないか」などの現状分析をおこないます。結果的に、パッケージングラインの梱包速度が遅いため、次工程以降に待機時間が生じているといったボトルネックを特定します。
制約が特定されたら、その制約を最大限に活用する方法を見つけます。この段階では、現在のリソースと能力の範囲内で最大限の成果を出すことに集中します。
例えば「パッケージングラインのプロセス上の無駄を省く」「作業員のスキルを向上させるトレーニングを実施する」などの方法が考えられます。
制約に合わせてほかのプロセスを調整することで、システム全体の効率を高めるステップです。
例えば「製造スピードや資材準備などのプロセスをパッケージングの速度に合わせて調整する」などが挙げられます。これにより、制約が原因で発生する次工程の待ち時間の短縮や、短期的な対策のために蓄積した過剰な在庫の削減が可能です。
制約が依然として全体の性能に大きな影響を与える場合、その制約を直接改善する方法を検討します。改善にあたっては、既存の条件や現状の変更を過度に考慮せず、制約の能力を増やすための投資などもおこないます。
例えば「追加の機材を導入する」「より効率的なパッケージング技術を採用する」「作業方法を変更する」などです。
制約が解消され、パッケージングの速度が改善されたら、システム全体を再評価します。新たなボトルネックが生じていないか確認し、もしあれば、同様のプロセスをその新たな制約に対しても適用します。この繰り返しにより、継続的にシステム全体の効率を向上させられます。
思考プロセスはTOC理論の一部で、複雑な問題を解決するために論理的思考を用います。このプロセスは、問題の根本原因を特定して効果的な解決策を策定するのに役立ちます。
具体的には以下の3ステップがあり、問題を戦略的かつ効率的に解決できるようになります。
こちらも事例を交えながらそれぞれ解説します。
このステップでは、現在の制約や問題点を特定します。目的は、システムやプロセス内の最も弱いリンク、つまり全体のパフォーマンスに最も大きな影響を与える要素を見つけ出すことです。これは、問題の根本原因を理解し、改善の焦点を定めるために不可欠です。
例えば、食品加工メーカーが新しい市場への進出に際して課題を感じているとします。
まず、現在のビジネスモデルや戦略のなかで、新しい市場への進出を阻害している要因を特定します。これにはさまざまな要因が考えられます。
新しい市場への進出を阻害している要因 | 具体例(イメージ) |
---|---|
製品の適合性 | 地元民の味覚や食文化に合わず、受け入れられない |
価格設定 | 進出先の経済水準に比べて販売価格が高い |
流通チャネル | 進出先の地元の小売業者や流通業者との関係構築ができていない |
ブランド認知度 | 新市場でのブランド認知度が低い |
地域の法規制 | 進出先の国や地域に特有の食品安全基準や輸入制限がある |
文化的な障壁 | 特定の食品成分が進出先の文化や宗教的信条に反する |
上記は一例ですが、このような観点から問題や制約を特定します。
特定された問題や制約をどのように解決または改善するかを考えます。これには、新しいアプローチ・プロセス・戦略または政策の提案が含まれる場合があります。このステップの目的は、特定された制約を克服し、システム全体の性能を最適化するための実行可能な解決策を見つけることです。
例えば「新しい市場での需要を満たすために製品を改良する」「よりローカライズされたマーケティング戦略を採用する」または「現地のパートナーシップを構築する」などです。この段階で、具体的で実行可能な変更計画を立てることが重要です。
最後に、策定した戦略や変更計画を実行するための詳細なステップを計画します。これには「必要なリソースの確保」「関係者とのコミュニケーション」「イムラインの設定」「リスクマネジメント」などが含まれます。
思考プロセスでの問題解決を成功させるためには、組織内の関係者が計画に沿って行動するだけでなく、各ステップの進捗を監視しながら適切に管理したり、必要に応じて調整をおこなったりするなど、すべての関係者の協力が不可欠です。
TOC理論を経営に取り入れることで得られるメリットは大きく四つあります。それぞれについて紹介します。
社内の業務プロセスの制約を特定して焦点を当てて改善することで、プロセス全体がスムーズになり、生産性やサービスの速度が向上します。また、ボトルネックを理解することで、無駄な作業や過剰な在庫の蓄積を防ぐなどの対策につながり、効率的な作業プロセスの構築ができます。
TOC理論では、社内のボトルネックを中心に資源を配分し、最も効果的に使用することを重視します。限られた経営資源(ヒト・モノ・カネ・情報)を最も効果的な改善策に集中投資することで、コストの無駄遣いを減らします。パフォーマンスを最大化してより高いリターンを得ることが可能になります。
個々の部門やプロセスだけでなく、組織全体の視点から最適化を図れます。これにより、部門間のシナジー(相乗効果)を生み出し、組織全体の目標達成に貢献します。全体最適化を目指すことで局所的な最適化に陥る事態を防ぎ、組織全体のパフォーマンス向上につなげられます。
TOC理論のアプローチを使うことで、組織内の意思決定プロセスを合理化し、人間特有の思考で生じる問題が解決できます。
思考プロセスは人間特有の認知の歪みや感情的な反応など、非論理的な行動が原因で生じる問題に対処するためのフレームワークであり、より客観的かつ効果的な解決策を導き出せます。また、チーム内のコミュニケーションを改善し、意思疎通を促進することも可能になります。
TOC理論を経営に取り入れることでさまざまなメリットがありますが、実施するにあたっては注意点があります。ここでは、TOC理論を取り入れる際の注意点を四つ紹介します。
TOC理論は、特に大規模な組織や多くの部門を持つ企業においては、管理の複雑性を増加させる可能性があります。複雑性を理解したうえで、取り組む際には評価指標をシンプルにすることを心がけましょう。改善の明確な目標を設定することで管理範囲が広がり過ぎないように注意が必要です。
TOC理論は特定の制約に重点を置いて改善活動をおこなうため、ほかの重要な要素や機会が見過ごされるリスクがあります。組織がボトルネックに集中しすぎると、創造性や革新的なアプローチが疎外される可能性があります。
特に、市場や競争環境の急速な変化や、短期的なトラブルへの迅速な対応が必要な場合などに起こり得るため、中長期経営計画を軸にした取り組みを意識しましょう。
TOC理論を導入する際には、既存のプロセスや文化に大きな変更を加える必要があることが多く、古参の役員や社員の抵抗を受ける可能性があります。そのため、組織内の人々が新しいアプローチに適応するためには十分な説明が必要です。また、プロジェクト体制の構築と定期的な進捗管理が欠かせません。
TOC理論は比較的高度な理論であり、適切に実施するためには十分な理解とトレーニングが必要です。経営初心者がこの理論を深く理解するには時間がかかる可能性があり、また間違った理解や適用は逆効果になるリスクがあります。
具体的なトレーニングには以下のような方法を検討しましょう。
TOC理論は、プロセスのスムーズな進行を妨げる要因となっているボトルネックを特定し、集中的に改善に取り組んで全体的なパフォーマンスを最適化する手法です。
TOC理論を経営に取り入れることで、生産性の向上や経営資源の効率的な運用などが可能です。一方で、過度な焦点化や経営層の一方的な改善推進による社員の反発などの恐れもあります。
TOC理論を経営に取り入れる際はこれらの点に注意し、全体のビジョンや目標に合わせて適切に調整しましょう。組織全体が同じ方向を向いて進めるよう努めることが大切です。
おすすめのニュース、取材余話、イベントの優先案内など「ツギノジダイ」を一層お楽しみいただける情報を定期的に配信しています。メルマガを購読したい方は、会員登録をお願いいたします。
朝日インタラクティブが運営する「ツギノジダイ」は、中小企業の経営者や後継者、後を継ごうか迷っている人たちに寄り添うメディアです。さまざまな事業承継の選択肢や必要な基礎知識を紹介します。
さらに会社を継いだ経営者のインタビューや売り上げアップ、経営改革に役立つ事例など、次の時代を勝ち抜くヒントをお届けします。企業が今ある理由は、顧客に選ばれて続けてきたからです。刻々と変化する経営環境に柔軟に対応し、それぞれの強みを生かせば、さらに成長できます。
ツギノジダイは後継者不足という社会課題の解決に向けて、みなさまと一緒に考えていきます。