業務効率化もキッチンカー開発も実現 吉谷機械製作所が変えた企業文化
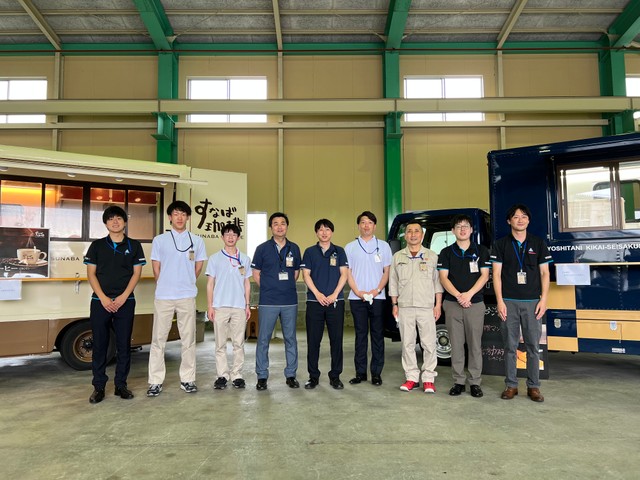
鳥取市の消防車メーカー・吉谷機械製作所4代目の吉谷勇一郎さん(43)は、社長就任後に製造原価の高止まりや需要減に危機感を覚え、専門家を招いて効率化に着手しました。後編では工場内のレイアウト変更や生産方式の刷新による業務効率化の舞台裏、キッチンカー製造や消防ポンプを利用した浚渫(しゅんせつ)システムの開発などの新規事業に迫ります。
鳥取市の消防車メーカー・吉谷機械製作所4代目の吉谷勇一郎さん(43)は、社長就任後に製造原価の高止まりや需要減に危機感を覚え、専門家を招いて効率化に着手しました。後編では工場内のレイアウト変更や生産方式の刷新による業務効率化の舞台裏、キッチンカー製造や消防ポンプを利用した浚渫(しゅんせつ)システムの開発などの新規事業に迫ります。
吉谷機械製作所は、ポンプ車市場では全国シェアの1割を占めるほど高い技術力を持っています。しかし、経理畑の吉谷さんは業務に非効率性を感じても、エンジニアを説得できませんでした。そこで社長に就任した2019年、中小企業基盤整備機構の「ハンズオン支援」で自動車メーカー出身の専門家を招き、抜本的な効率化に取りかかります(前編参照)。
ハンズオン支援では、現場と専門家が一丸となって改革を進めていきます。例えば「コストの削減」と「価値の最大化」といった両面から製造プロセスを改革するため、グループワークでバリューエンジニアリング(VE)に取り組みました。
そうして実現した業務効率化の一つが、作業スペースのレイアウト変更でした。サイズが大きい消防車の仕掛かり品は、作業中の移動距離を最小限に抑えることが時間短縮のポイントになります。
改革前の工場内は無駄な移動が生じるレイアウトでした。工程の順序が意識されず、工場内を右往左往しながら作業を進めている状態だったのです。
そこで、以前はなんとなく決められていた工場内のレイアウトを、工程間の移動が最短になるよう合理的な計画にもとづいて工程順に再配置しました。変更後は順々に隣のスペースに移るだけで工程間の移動が済むようになり、1台を製造する際の平均移動距離が320メートルから36%減の204メートルに短縮されました。
もう一つの改善策が生産方式の刷新です。改革前はポンプなど消火活動に必要な設備を、車の骨組み(シャシー)に直接取り付けていました。しかし、この方式は、シャシーが納入されなければ作業に着手できない点がネックでした。
↓ここから続き
シャシーの注文は案件の受注後に行われていましたが、納入されるまで1〜2カ月の待ち時間が生じていたのです。
注目したのが、部分的に採用されていた「モジュール方式」です。この生産方式では、まず消火設備が詰まったモジュールを組み上げます。そして、最後にモジュールをシャシーに積載して消防車を完成させます。
シャシーの納入を待たず作業に着手できるため、納期にゆとりが生まれてキャパシティーオーバーが起こりにくくなるというわけです。
シャシーを(消防設備を製造する)工場に入れて作業する必要がなくなり、工場内のスペースにもゆとりが生まれました。その結果、同時並行できる業務量が8台から16台に倍増して、効率化が飛躍的に進みました。
そのほか工程間検査による手戻りの予防、工場内通路の拡張がもたらした運搬効率の向上など様々な施策を積み重ね、21年には作業時間の13.5%削減を達成します。
一連の取り組みは外注費の削減にもつながり、2千万円以上のコストダウンが実現しました。「不可能と思われていた改革を成し遂げることができました」と吉谷さんは語ります。
効率化の道筋がついてからは利益確保の見通しが立つようになり、中長期的なビジョンを考える余裕が生まれました。「消防車市場は縮小が見込まれており(前編参照)、新市場の開拓を模索する必要がありました」
そこで、21年に新規事業としてキッチンカーの製造に乗り出しました。「車台に設備を搭載する」という点で、消防車とキッチンカーは製作工程が類似しています。自社の強みを発揮できる市場だと考えたわけです。
また、消防車の製造は入札シーズンにあたる秋に業務が集中していましたが、キッチンカーは年間を通じて需要が見込めます。キッチンカー事業には労働時間の平準化という狙いもありました。
キッチンカーの床面には木材や樹脂がよく使われているといいますが、吉谷機械製作所では「縞板」という消防車用のアルミ製の板を使っています。「消防現場で証明された滑落防止性能と耐久性が特徴です」
キッチンカー事業には続々と問い合わせが寄せられているものの、半導体不足による車台の品薄がネックになっているため、主に中古車の改造で対応可能な案件を受注しています。納品事例はまだ数件にとどまっていますが、吉谷さんは新規事業に手応えを感じています。
「法令の縛りが厳しい消防車に比べれば、キッチンカーは自由度の高さが魅力です。工夫次第で原価を下げながら品質を保ちやすく、採算性を維持できます。第二の経営の柱として期待しています」
未知の新領域に進出する可能性も見えてきました。現在、同社では放水圧力を高めるために使用されてきた技術を、浚渫という土木工事に転用するために、「小型エジェクター」という専用装置の開発を進めています。
浚渫とは水底に堆積した土砂を除去する工事で、河川や港湾の管理において不可欠とされています。従来は大型の機材を使った大規模工事が必要なため、タイムリーな浚渫は困難とされてきました。
一方、吉谷機械製作所が小型エジェクターを提供している複数社共同の開発プロジェクト「消防ポンプを利用したコンパクト浚渫システム」では、装置の小型化が図られた結果、日常的に浚渫を行っても低コストで済む可能性が期待されています。
21年には、海底火山の噴火で生じた軽石の除去作業で実証実験した結果、一定の成果が出ました。現在、さらなる実証データの蓄積が浚渫工事で進められているほか、海藻を食い荒らすムラサキウニの駆除や土砂災害からの復旧工事など幅広い応用の可能性が見えています。
キッチンカーや浚渫用の装置開発など新規事業を進める背景には、コロナ禍の教訓がありました。海外からの物流が途絶え、シャシーの納入が困難になったため、製造の見込みが立たない場面が生じていたのです。
「このままではまずい、という意識が社内に広がっていきました。ある意味、新規事業の立ち上げに追い風が吹いていたと思います。100年近く消防・防災関連事業に専念してきた会社なので、平時では新規事業に頭を切り替えることに苦労したでしょう」
業務効率化や新規事業の開発を経て、社内の空気も変わり始めました。吉谷さんは「以前はできない理由を探すくせが社内に蔓延していました。過去の常識にとらわれていたのでしょう。改革によって様々な壁を破るうちに『やればできる。まずやってみよう』という雰囲気が社内に広がっていきました」。
現在は一人ひとりが「もっとよい方法があるはずだ」と問題意識を持って仕事に取り組んでおり、改革を自律的に継続できるような企業文化が芽生えているといいます。
「会社を良くするために積極的な行動を取ってくれるなど、会社愛を持つ『人財』が生まれています。ベテランから若手まで幅広い層の社員が、頼りになるキーマンとして成長中です」
社長就任から間もない吉谷さんにとって、経営の片腕になるような人材が頭角を現し始めています。
「社長に就任してからは、毎年春に会社のビジョンを社内で共有する経営計画発表会を催しています。社長としての想いが徐々に伝わると、新しい取り組みに社員が耳を傾けてくれるようになりました」
吉谷機械製作所は5年後の27年に100周年を迎えます。節目を目前に控え、吉谷さんは次世代のビジョンについてこう語りました。
「100年近く事業を続けていれば、時代に合わない面も現れてきます。現に消防車市場は厳しさを増しています。既存事業だけに特化するのではなく、『人々の笑顔のため、安心・安全を届ける』という経営理念のもとで視野を広く持つことが私に求められています」
「多角化の必要性を切に感じた事態がコロナ禍でした。既存事業とのシナジーを備えた次世代の事業展開を進めていきたいです」
(続きは会員登録で読めます)
ツギノジダイに会員登録をすると、記事全文をお読みいただけます。
おすすめ記事をまとめたメールマガジンも受信できます。
おすすめのニュース、取材余話、イベントの優先案内など「ツギノジダイ」を一層お楽しみいただける情報を定期的に配信しています。メルマガを購読したい方は、会員登録をお願いいたします。
朝日インタラクティブが運営する「ツギノジダイ」は、中小企業の経営者や後継者、後を継ごうか迷っている人たちに寄り添うメディアです。さまざまな事業承継の選択肢や必要な基礎知識を紹介します。
さらに会社を継いだ経営者のインタビューや売り上げアップ、経営改革に役立つ事例など、次の時代を勝ち抜くヒントをお届けします。企業が今ある理由は、顧客に選ばれて続けてきたからです。刻々と変化する経営環境に柔軟に対応し、それぞれの強みを生かせば、さらに成長できます。
ツギノジダイは後継者不足という社会課題の解決に向けて、みなさまと一緒に考えていきます。